汽轮机主轴(转子)是工业汽轮机中的核心部件,工作环境恶劣,旋转速度高、应力集中部位多。一旦出现裂纹不但很难修复,还容易造成转子转动的不平衡。主轴(转子)将蒸汽的热能和动能转变为旋转的机械能并传递给发电机进行发电,承载高压、高温及动力载荷,其轴瓦位置的质量直接决定着汽轮机的运行稳定性、安全性和维护保养周期,因此轴瓦位置的加工工艺、加工设备和加工质量一直困扰着主机厂、配套商和维修服务商。两端的轴颈部位,承受着整根转子的重量和连续的摩擦力,因此轴颈加工也是整台转子加工的重中之重。
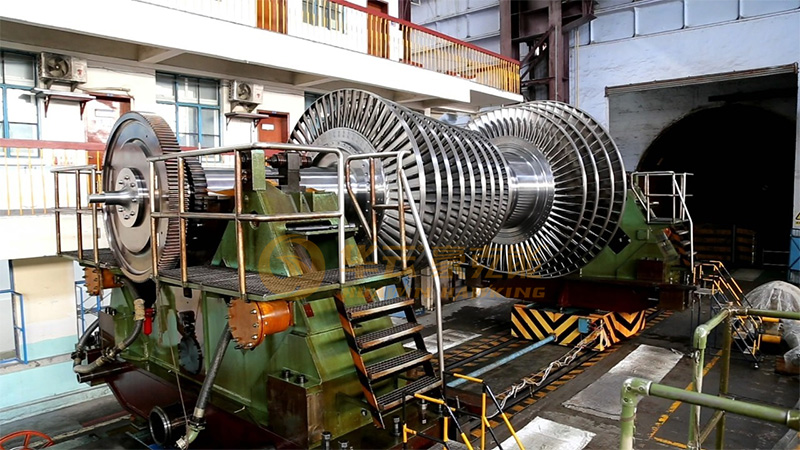
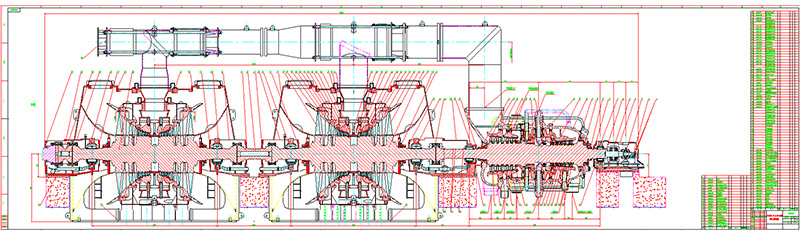
转子的表面性能(形位公差、几何精度﹑表面粗糙度等)由机械加工来实现。表面精度低会影响安装精度,同时在使用过程中易出现磨损﹑剥蚀﹑融合粘结、表面材料转移或因加工应力造成的疲劳断裂源,从而使零件的使用寿命缩短。选择合适的机械加工工艺,对实现转子的加工要求,提升转子的质量和使用寿命具有重要的意义。
1. 转子加工要求
轴瓦一般采用碳钢及中碳合金等金属材料,表面粗糙度要求Ra值≤0.4μm。
按API612标准要求,转子轴颈加工的表面粗糙度Ra≤0.4μm、圆柱度和电跳量应≤0.006mm。
2. 传统加工工艺及缺陷
▶ 一种方式为先精车后表面粗糙度Ra1.6,然后进行磨床磨削或者砂带手工抛光,表面粗糙度达到Ra0.4 -0.8之间。
缺点:表面质量不够理想且手工研抛劳动强度大、安全性差。磨抛工艺无法实现Ra值≤0.2μm的最优表面质量,无法彻底消除切削加工的刀痕(波峰),刀痕(波峰)锐边对轴承副产生局部“铲刮”磨损而削弱密封性能,出现支撑失效和气封失效,严重生产和人身安全等。
▶ 第二种方式为精车后进行表面滚压。
缺点:不可重复多次滚压。操作不慎会使表面硬化层起皮、起皱,甚至剥落,且刚性的硬挤压会对精密机床的精度带来非常不利的影响。
3. 采用豪克能镜面加工工艺
▶ 精车后Ra1.6 → 采用豪克能镜面加工后Ra0.2以内。
豪克能金属表面加工的工作原理是利用金属在常温状态下的冷塑性特点,运用豪克能对金属零件的表面进行每秒3万次左右的高频冲击,强化和微小的形变处理使零件表面达到更理想的表面粗糙度要求。同时在零件表面产生压应力,提高零件表面的显微硬度、耐磨性、疲劳强度和疲劳寿命。
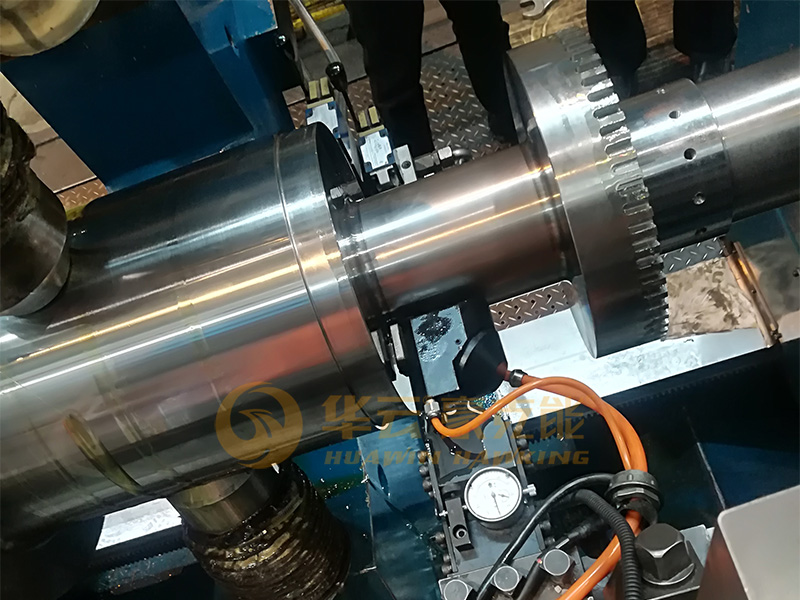
▶ 加工效果
粗糙度:Ra值≤0.2μm,完全满足技术要求。
硬 度:提高20%
电跳量:优于标准值25%,完全满足技术要求
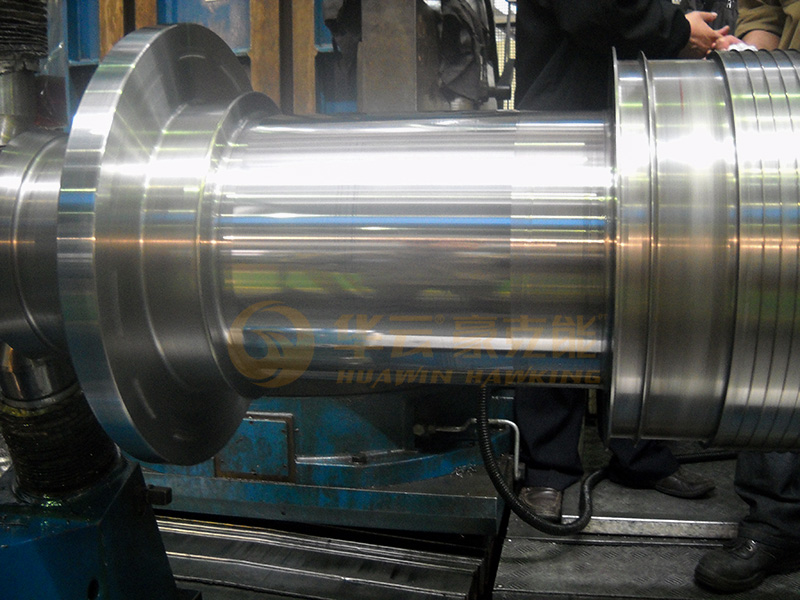
▶ 性能提升
采用豪克能技术取代原磨削工艺,粗糙度提升3个等级、消除微观铸造缺陷消除局部“铲刮”磨损、硬度提高20%、电跳量优于标准值25%,取代磨抛工艺,保证质量、生产效率和降低维护成本,完全设计标准。
豪克能加工位置摩擦系数降低25%、硬度提高20%,耐磨性能和密封性能提升1倍以上,在大修和小修维修保养过程中,没有磨损划伤,仅有划痕,通过常规抛光即可快速实现维保,缩短维保周期,降低成本,提高产值。
