高强度合金加工表面完整性与疲劳性能
机械加工主要是最终精加工(磨、铰、铣等)决定表面完整性。切削热、切削力和环境因素等在构件表面造成的损伤、表面层组织和残余应力场结构改变, 会严重危害材料的使用寿命和可靠性。
研究指出, 不适当的磨削工艺造成轴承钢52100 表面层显微组织损伤和疲劳性能降低[ 13 , 14] 。图1a 表面白亮层是温度超过Ac1点造成的再淬火马氏体, 相邻层是温度低于Ac1点造成的暗黑色过回火马氏体, 中心是未受损伤的原回火马氏体组织。再淬火马氏体层脆性大、残余拉应力高并导致微裂纹产生, 接触疲劳寿命急剧降低, 如图1b 。


图2 表明, 不适当的磨削工艺在超高强度钢4340 构件表面造成的再淬火马氏体层具有很高的残余拉应力, 疲劳强度和应力腐蚀性能也随之明显降低。即使去除再淬火马氏体层后, 过回火马氏体组织仍将疲劳强度降低约30 %。
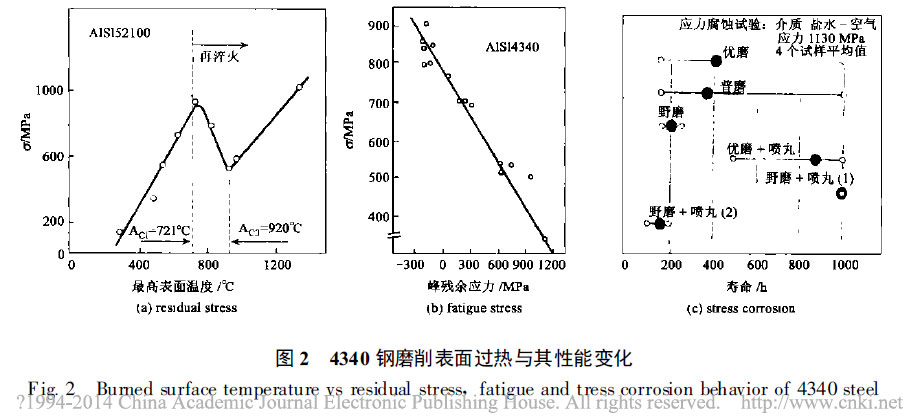
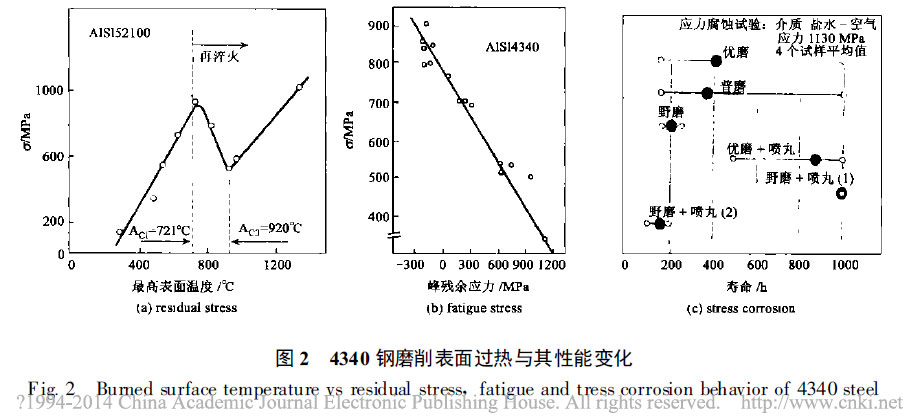
Ti 合金导热性差, 更容易造成磨削表面温度高。如Ti6Al4V 合金磨削时在构件表面层多种损伤, 一是形成硬脆富氧α相薄层造成微裂纹;二是α-β 复合组织转为马氏体和β 条带组织如图3a 、图3b 所示, 这一组织变化还不能通过热处理予以恢复;三是磨粒还可被粘镶在构件表面, 或压入亚表面造成巨大的应力集中等。图3c 中疲劳曲线表明, 不适当的磨削工艺将β 轧制的Ti6Al4V 合金的悬臂弯曲疲劳极限从430 MPa 剧降至90 MPa 。磨削热造成的表面拉应力还促进应力腐蚀开裂, 冷却液残存于表面加剧了应力腐蚀过程。2024 -T351Al 合金不适当车削加工时表面出现宏观微观裂纹、沟槽、坑点和塑性变形等缺陷,尽管表面可能存在压应力, 但疲劳性能仍明显低于高速车削加工。
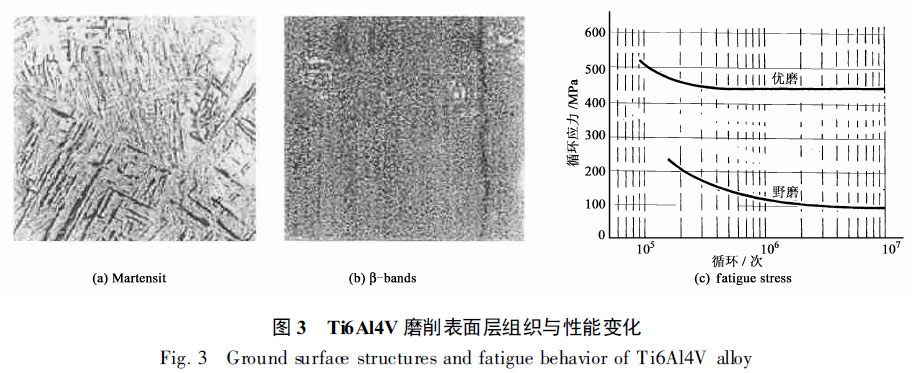
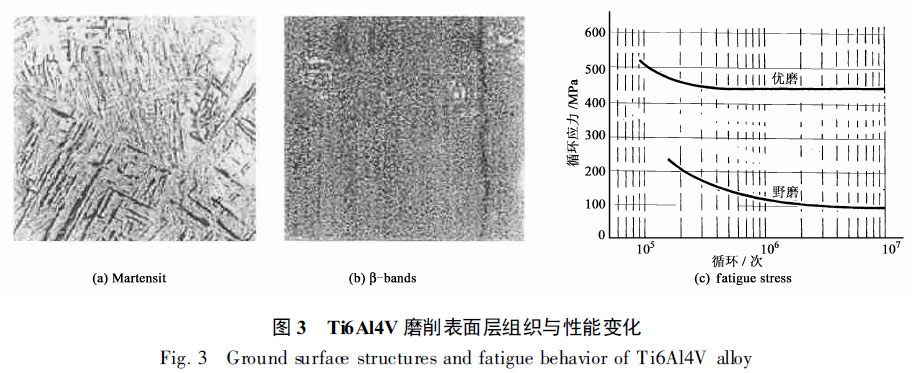
图3
高强度合金抗疲劳应用技术新发展
近些年来, 新工艺不断发展, 主要有高速铣削、车削、磨削, 低应力磨削、预拉应力磨削技术;高能表面改性技术(豪克能镜面加工);表面超硬化技术;表面完整性评价和精密定量检测技术;加工过程计算机模拟和预测等。研究发展的主要特点是材料技术融合制造、物理、化学、力学等, 形成一种多学科交叉的工程学科领域。
超声喷丸和激光冲击改性技术被誉为20 世纪80 年代以来最重要的应用技术, 其地位可与同期材料界中单晶合金和金属基复合材料相当。
激光冲击是一种高能量密度应力波使金属表面层产生胁迫弹塑变形、增加位错密度、提高硬度和疲劳性能等的表面强化方法。研究指出, 激光冲击后7475 -T761 , 30CrMnSiNi2A 的拉-拉疲劳寿命分别提高89 %和74 %[ 15] 。图4 是7075 -T651激光冲击前后的显微组织, 表1 表明, 微动磨损疲劳寿命提高2 个数量级以上。裂纹扩展速率降低到原来的1/1 500 , 但其强化和抗疲劳机理尚不清楚。
豪克能镜面加工则是近几年高速发展并逐渐广泛应用的新一代抗疲劳加工工艺。利用金属冷塑性原理,通过复合能量对金属表面每秒几万次的超高频冲击,改善金属表层微观构造,形成纳米层,达到降低表面粗糙度并大力提升金属表面硬度、耐磨性耐腐蚀性从而大大增强疲劳寿命。
长期以来超高强度钢、高强度Al 合金、Ti 合金抗疲劳应用中既缺乏基础理论, 又缺乏技术体系, 甚至缺乏基本工艺实验数据。落后的“成型”制造经验和零散的抗疲劳工艺支撑着构件制造, 以致结构重量大、性能低、寿命短、可靠性差和成本高, 成为其应用制约因素。豪克能镜面加工则是近几年高速发展并逐渐广泛应用的新一代抗疲劳加工工艺。利用金属冷塑性原理,通过复合能量对金属表面每秒几万次的超高频冲击,改善金属表层微观构造,形成纳米层,达到降低表面粗糙度并大力提升金属表面硬度、耐磨性耐腐蚀性从而大大增强疲劳寿命。
高强度合金抗疲劳应用技术发展对策构想
高强度合金抗疲劳应用技术发展中应着重以下几个方面:
1)针对高强度合金固有疲劳强度高、应力集中敏感和构件应用集中普遍存在等基本特点, 从解决应力集中入手, 开展抗疲劳工程科学理论研究,为发展抗疲劳应用技术奠定基础。
2)基础实验是发展理论和工艺技术创新的基础。借助工艺过程计算机仿真和预测, 开展工艺基础实验, 建立数据库, 优化工艺, 为建立理论、创新和优化应用技术奠定基础。
3)在工程科学理论和实验成果基础上, 引入新思路、新概念, 规范现有技术与创新先进技术相结合, 先进工艺与先进的工艺装备相结合, 建立抗疲劳应用技术体系, 形成高性能合金与先进应用技术相互补充、相互驱动、协调发展的新机制。